Анализ потребления электроэнергии в отраслях экономики России показывает, что предполагаемые структурные сдвиги в промышленности происходят крайне медленно и почти не влияют на объемы спроса на ТЭР. Обрабатывающие отрасли остаются наиболее энергоемким комплексом и сохраняют свои характеристики спроса уже много десятилетий. Нарастание энергосберегающих усилий, охватывающее всю страну, почти не затронуло отрасль. Это связано в первую очередь с эксплуатацией накопленного парка технологических машин, сконструированных в эпоху дешевой энергии, и продолжающих свою технологическую жизнь в настоящее время. Более того и новые технологические линии конструируются на основе Правил, принятых давным давно. (Для примера укажем, что Нормы технологического проектирования электростанций разработаны и приняты в 1979 году).
В связи с этими обстоятельствами представляется целесообразным направить усилия на инженерную поддержку энергосбережения технологической среде.
Оптимизация схемы обработки резанием как инструмент энергосбережения
Гольдшмидт М.Г., доцент ТПУ, к.т.н., эксперт НП «Региональный центр управления энергосбережением»
Козарь Д.М., аспирант ТПУ
На примере конструирования технологических машин рассмотрены некоторые вопросы инженерного энергосбережения.
Несовершенство многих технологических процессов и машин в части энергосбережения долгие годы «не замечалось» отечественными конструкторами и технологами. Непоколебимая уверенность наших специалистов в безграничности энергетических ресурсов России не способствовала модернизации процессов и оборудования и выживанию в жестокой конкурентной борьбе.
В технической литературе, к сожалению, немного работ посвященных инженерным проблемам энергосбережения. И это – при непрерывно повышающейся стоимости энергоносителей!
А между тем может оказаться полезной даже дискуссия на тему энергосбережения; она способствует повышению как общей технической культуры, так и, что особенно важно, культуры использования энергии.
Длительное время на кафедре «Автоматизация и роботизация в машиностроении» Томского политехнического университета ведутся разработки технологических машин различного назначения, а Некоммерческое партнерство «Управление энергосбережением» - теорией и практикой рационального энергопотребления.
Особенно остро проблема энергосбережения возникла при разработке технологии и технологических машин для дробления резины при утилизации изношенных покрышек. Известно, что переработка покрышек в гранулы размером от 0,5 до 1,5 мм позволяет весьма эффективно использовать их как компонент напольного покрытия при строительстве спортивных площадок, «нескользких» дорожек и т.п.
Анализ задач возникающих при разработке оригинальной конструкции технологической машины (решение о выдаче патента на полезную модель по заявке №2010149939/105(72117)) показал, что затраты на энергию при эксплуатации машин играют главенствующую роль. Следовало изучить, на сколько обоснованным является то обстоятельство, что в большинстве машин для переработки покрышек средних размеров мощность двигателя превышает 60кВт.
Вероятно, при конструировании машин преследовалась одна цель – выполнение машинной задачи по обеспечению показателя назначения.
А между тем оказался возможным другой подход, состоящий в том, чтобы допустить некоторое снижение производительности за счет существенного повышения эффективности расхода энергии. Таких примеров можно приводить множество.
Рассмотрим содержание некоторых этапов работы по конструированию машин в той или иной мере связанной с энергосбережением.
- Разработка концептуальной схемы устройства.
Разработка концептуальной схемы изделия имеет большое значение, так как после выполнения этого этапа процесс проектирования переходит в следующую стадию – процесс конструирования, который является более определенным, поддающимся алгоритмизации. Творчество уступает место системе, фантазия – порядку.
Любая машина, как правило, может быть построена на основе различных принципов. Применительно к машинам для получения гранул этот процесс мог бы быть реализован по крайней мере тремя путями:
- путем замораживания предварительно разрезанных на части покрышек и разрушения сжатием; однако использование жидкого азота энергетически требует больших затрат;
- путем пропускания предварительно разделенных частей покрышки через устройство аналогичное мясорубке;
- по схеме лезвийной обработки, например фрезерованием, по которой работает большинство машин;
- Выбор схемы резания
Рис. 1. Схемы резания: а) одинарная; б) групповая
Под схемой резания понимают картину постепенного изменения формы и размеров обрабатываемой поверхности или способ распределения работы (припуска) между режущими зубьями [1]. Это положение справедливо для многих видов обработки резанием. Ниже оно наглядно иллюстрируется применительно к протягиванию.
Существуют, как известно, две схемы резания при протягивании: так называемая обычна и переменная. При обычной схеме каждый режущий зуб срезает широкий, но тонкий слой металла (рис. 1, а). Схема переменного резания отличается тем, что каждый зуб срезает короткий, но толстый слой.
При обычной или одинарной схеме резания поверхность образуется, как правило, методом подобия или профильным методом. Контур режущей кромки каждого зуба здесь подобен профилю окончательно обработанной поверхности.
Многочисленными экспериментами показано, что чем больше толщина срезаемого слоя а (рис. 2) тем меньше удельная сила (давление) резания [1], и собственно, меньше требуется относительная мощность привода.
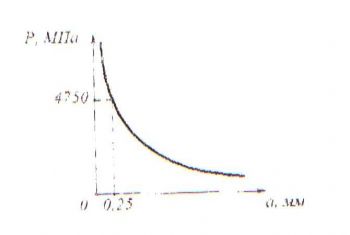
Рис. 2. Зависимость давления резания от толщины срезаемого слоя
- Решение задач динамики
Синтез кинематической схемы и системы управления как и ранее, на двух предыдущих этапах, проводится с учетом минимизации энергопотребления.
Любое устройство реализует какой-либо закон движения подвижных органов.
На примере можно показать сколь ответственным с точки зрения энергосбережения является выбор кинематики проектируемого устройства: какой из законов разгона и торможения задан в устройстве для движущегося органа.
При решении проектных задач в условиях неопределенности используют коэффициенты, отражающие свойства данного класса машин. При оценке динамического момента, например, принимают, что разгон и торможение происходят с одинаковым ускорением:
,
здесьΨ - соответственно углы поворота при разгоне, торможении и суммарном перемещении. В этом случае график перемещения подвижного элемента имеет вид, представленный на рис. 3.
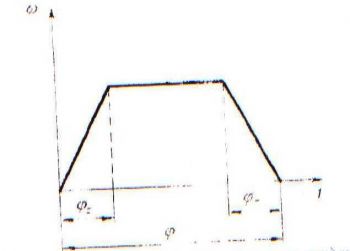
Рис. 3. Схема изменения скорости поворота подвижного узла
Очевидно, чем меньше принятый коэффициент тем больше нагрузки испытывает привод и, следовательно, возрастает потребляемая мощность.
В связи с изложенным можно утверждать, что работать фрезой (как, впрочем, и другим вращающимся и имеющим большую массу инструментами) с точки зрения рациональности расхода энергии нецелесообразно.
Мощность привода главного движения (вращения фрезы) можно оценивать по формуле [2]:
Ψ
ω – номинальное значение угловой скорости, м/с;
Ψ – угловое перемещение элемента рад;
m – масса вращающихся частей, кг;
r – радиус действия инерционного момента, м;
k– коэффициенты конструкции.
Согласно приведенной формуле уменьшение коэффициента в 10 раз (до требует пропорционального увеличения мощности привода, а трехкратное увеличение частоты вращения подвижного элемента, - увеличивает требуемую мощность в 27 раз!
Заключение. В процессе проектирования приемами показанными выше, устанавливаются характеристики изделия, по предварительным расчетам обеспечивающие рациональное энергопотребление. Следующим шагом может быть учет суммарных затрат и их минимизация, выполняемые так как показано на рис. 4.
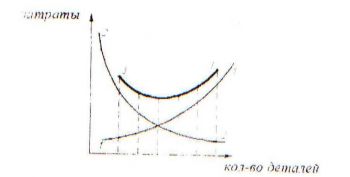
Рис. 4. Суммарные затраты по определению оптимальных условий проектирования, изготовления и эксплуатации технологических машин:
1-1 – затраты энергии при эксплуатации устройств для утилизации покрышек; 2-2 – затраты на изготовление гранул (крошки) с использованием анализируемой группы оборудования; 3-3 – суммарные затраты.
Приведенные примеры показывают, что в каждом элементе конструирования возможно выделить инженерные средства управления энергосбережением. Повышение конкурентоспособности отечественных технологий и изделий возможно при внимательном отношении к вопросам инженерного энергосбережения.
Литература
- Инозмецев Г.Г. Проектирование металлорежущих инструментов: Учебн. пособие для вузов по специальности «Технология машиностроения, металлорежущие станки и инструменты». – М.: Машиностроение, 1984. -272с.
- Проектирование и разработка промышленных роботов/ С.С. Аншин, А.В. Бабич, А.Г. Баранов и др.; под общ. ред. Я.А. Шифрина и П.Н. Белянина. – М.: Машиностроение, 1989. – 272 с.